.
14.05.2014
The four RS-25 engines selected for the debut launch of the Space Launch System (SLS) are veteran Space Shuttle Main Engines (SSME) with a rich history of successful flight. The four engines will be delivered to the Michoud Assembly Facility in the second half of 2015, ahead of being installed on the core stage of the Exploration Mission -1 (EM-1) SLS.
SLS EM-1 Engine Set:
The RS-25D, or SSME as it is more commonly known, helped push the Space Shuttle fleet uphill during a 30 year career that resulted in only one major malfunction during its flight history - namely STS-51F (ME-1), resulting in a safe Abort To Orbit (ATO).
Following the decision to retire the Shuttle once the International Space Station had been assembled, the engines were set to live on with the Ares I Upper Stage. However, problems with the requirement for air-starting the engine for second stage flight altered NASA’s direction towards the J-2X.
With the Constellation Program (CxP) culled from NASA’s forward path, the realigned deep space exploration goals called for a Heavy Lift Launch Vehicle (HLV), utilizing the best hardware from the defunct CxP and esteemed Shuttle Program.
As such, the remaining set of RS-25Ds from the Shuttle Program were given one final role, to launch the SLS before ending their lives when the Core Stage is destroyed post-launch via a destructive re-entry.
.
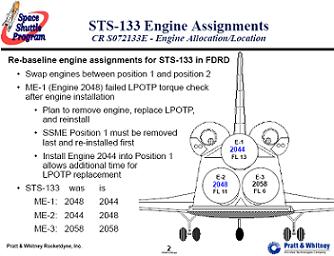
A total of 15 RS-25Ds left the Kennedy Space Center (KSC) for their new role, arriving at the Stennis Space Center in 2012.
The shipped engines included all nine of the last SSMEs to fly with the Space Shuttle. These engines performed admirably, with Discovery flying Main Engine 1 (ME-1) – serial number 2044, ME-2 – 2048 and ME-3 – 2058 during her final mission, STS-133.
For Endeavour’s swansong, ME-1 – 2059, ME-2 – 2061, and ME-3 – 2057 helped begin the flight phase of the successful STS-134 mission, while Atlantis closed out the Space Shuttle Program, flying with engines ME-1 – 2047, ME-2 – 2060 and ME-3 – 2045 during STS-135.
In preparation for this new role for the famous engines, Stennis engineers built a new 7,755-pound thrust frame adapter for the A-1 Test Stand, in order to enable testing of the RS-25s ahead of their role on SLS’ core.
.
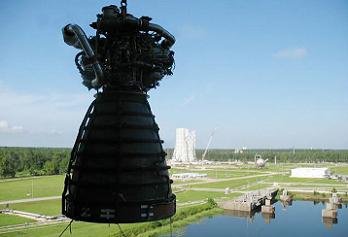
The first engine that will grace the test stand for the opening tests of the RS-25 for SLS will be Engine 0525.
This engine never flew in space, as it was one of two development engines used for component testing on Stand A-2 to support shuttle flights – 0528 was the second development engine.
Final testing – using these units was conducted in 2009 – with engine 0525 earmarked for any hot-fire tests that may have been required to support the final STS missions during 2010.
According to L2 information, the assembly of engine E0525 is now scheduled for completion on May 22.
.
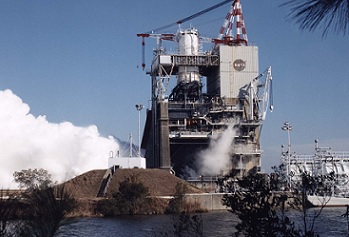
The Firing Readiness Review for the A-1 test stand is scheduled for May 28, and engine E0525 is to be installed on the A-1 stand on June 2. The first test firing is still scheduled for July 8.
This will officially mark the first live testing of the RS-25s towards their role with SLS, as preparations for the December 15, 2017 debut of the HLV begin to pick up the pace.
In a sign of the advancing path towards that first launch, L2 information has confirmed NASA’s Liquid Engine Office has now selected the first four engines that will loft the monster rocket uphill.
.
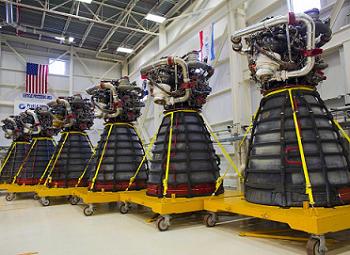
The four engines – ME-2045, ME-2056, ME-2058, and ME-2060 – are all established Shuttle veterans with numerous successful missions under their belts.
Per L2 SSME Flight Readiness Review (FRR) and Green Book documentation, ME-2045 – the most experienced engine set to fly on EM-1 – flew on STS-89, 95, 92, 102 and 105 in its Block IIA configuration, along with STS-110, 113, 121, 118, 127, 131 – and the final shuttle mission with Atlantis on STS-135 – in its Block II configuration.
The upgrade path for the SSME saw the Block IIA as an intermediate upgrade from Block I, after which followed the full Block II configuration. Changes made to the engines did not affect either the engine or the powerhead serial numbers.
.
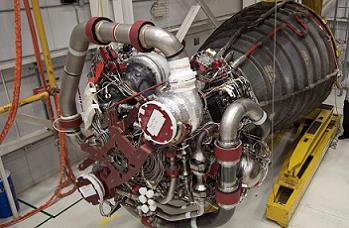
The main change from Block IIA to Block II was the use of a new High Pressure Fuel Turbopump (HPFTP). However, there were also other changes made during this process, per the “SSME Bible” (L2).
In contrast, the Block I to Block IIA upgrade involved new engine serial numbers, such as the main combustion chamber, which was new. However, they were mated to the old powerheads, whose serial numbers did not change.
The next engine selected for EM-1 – ME-2056 – flew on STS-104 and 109 in its Block IIA, before becoming involved in STS-114 and STS-121 as a Block II engine.
ME-2058 and ME-2060 are newer engines, both flying only in their Block II configuration.
ME-2058 flew with STS-116, 120, 124, 119, 129 and 133, while ME-2060 helped push STS-127, 131 and STS-135 into orbit.
.
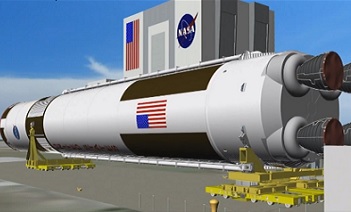
These four engines are scheduled to be delivered from their current home at the Stennis Space Center to MAF at one-month intervals beginning in September 2015.
SLS will see the engines being installed into the core at MAF, ahead of being shipped to the Kennedy Space Center (KSC).
After the last of those engines are delivered in December 2015, four more engines will be prepared and tested as contingency engines, to be available in case one or more of the first four engines need to be replaced.
These contingency engines will be ME-2047, ME-2059, ME-2062, and ME-2063.
.
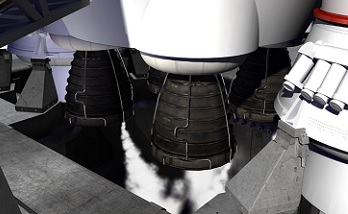
Providing there are no problems with the EM-1 set, these next four engines are now all-but confirmed as being the engine set for SLS’ second mission into space, which may become a specific payload mission in 2019.
This intermediate mission may debut the new Exploration Upper Stage (EUS) ahead of SLS’ third mission, which is known as Exploration Mission -2 (EM-2).
EM-2 is set to be the first launch of a crewed Orion, on a mission to explore a captured asteroid near the Moon.
(Images: Via NASA and L2 content from L2′s SLS and SSME specific L2 sections, which includes, presentations, videos, graphics and internal – interactive with actual SLS engineers – updates on the SLS and HLV, available on no other site.)
(L2 is – as it has been for the past several years – providing full exclusive SLS and Exploration Planning coverage.
.
Quelle: NSC
.
Update: 12.06.2015
.
We have Ignition: NASA Space Launch System RS-25 Engine Fires Up for Third Test in Series
The RS-25 engine fires up at the beginning of a 500-second test June 11 at NASA's Stennis Space Center near Bay St. Louis, Mississippi. Four RS-25 engines will power the core stage of NASA's new rocket, the Space Launch System.
Credits: NASA/Stennis
.
Ladies and gentlemen, we've started our engine. An RS-25 engine fired up for 500 seconds June 11 at NASA's Stennis Space Center near Bay St. Louis, Mississippi.
Four RS-25 engines will power NASA's new rocket, the Space Launch System, at speeds of 17,500 mph -- 73 times faster than the top speeds of an Indianapolis 500 race car -- to send astronauts on future missions beyond Earth’s orbit, including to an asteroid and ultimately to Mars.
This is the third firing of an RS-25 development engine on the A-1 test stand at Stennis. The first RS-25 test in this series was conducted Jan. 9, and the second was May 28. Four more tests are planned for the current development engine.
"While we are using proven space shuttle hardware with these engines, SLS will have different performance requirements," said Steve Wofford, manager of the SLS Liquid Engines Office at NASA's Marshall Space Flight Center in Huntsville, Alabama. The Marshall Center manages the SLS Program for the agency. "That's why we are testing them again. This is a whole new ballgame -- we need way more power for these engines to be able to go farther than ever before when it comes to human exploration. And we believe the modifications we've made to these engines can do just that."
The first flight test of the SLS -- designated as Exploration Mission 1 -- will feature a configuration for a 70-metric-ton (77-ton) lift capacity and carry an uncrewed Orion spacecraft beyond low-Earth orbit to test the performance of the integrated system.
"We have several objectives that will be accomplished during this test series, which will provide critical data on the new engine controller unit, materials and engine propellant inlet pressure conditions," Wofford added.
The new engine controller unit, the "brain" of the engine, allows communication between the vehicle and the engine, relaying commands to the engine and transmitting data back to the vehicle. The controller also provides closed-loop management of the engine by regulating the thrust and fuel mixture ratio while monitoring the engine's health and status. The controller will use updated hardware and software configured to operate with the new SLS vehicle avionics architecture.
The test series will show how the RS-25 engines will perform with colder liquid oxygen temperatures; greater inlet pressure due to the taller SLS core stage liquid oxygen tank and higher vehicle acceleration; and more nozzle heating due to the four-engine configuration and its position in-plane with the SLS booster exhaust nozzles. New ablative insulation and heaters also will be tested during the series. Aerojet Rocketdyne of Sacramento, California, is the prime contractor for the RS-25 engine work.
As the SLS evolves, it will provide an unprecedented lift capability of 130 metric tons (143 tons) to enable missions even farther into our solar system to places like Mars.
Quelle: NASA
5510 Views