14.12.2019
Rosalind meets Rosalind
The work of Dr Rosalind Franklin (1920-1958) is well known for being central to the discovery of the iconic double-helix structure of DNA, the fabric of life as we know it on Earth. More than half a century later, she also inspired the name of ESA’s ExoMars rover, scheduled to launch in 2020 and start its exploration of the Red Planet in 2021. But the lasting imprint Rosalind left on her family also inspired her younger brother to name his own daughter Rosalind.
After learning that the rover had been named in honour of her aunt – the result of a public competition led by the UK Space Agency – and also sharing the same name, Rosalind Franklin reached out to ESA, curious to learn more about the mission. Last month, she visited ESA’s technical centre in the Netherlands and is pictured here meeting the 1:1 scale model of the Rosalind Franklin ExoMars rover for the first time.
Rosalind said: “I was overwhelmed to see the rover and to meet the extraordinary scientists that have dedicated years to the development of the project, bringing it from concept to reality, and recognising my Aunt Rosalind’s contribution to science by naming it after her. It was truly moving and filled me with pride and appreciation. It was an amazing day of learning and discovery and I know she would feel so honored and full of admiration towards everyone involved.”
ExoMars mission experts were on hand to answer her questions and to explain more about how the rover will be driven across the martian surface, and the science experiments it will carry out. One of the unique aspects of the rover is its two metre long drill that will retrieve underground samples for analysis in its onboard laboratory, where it will be able to sniff out signatures of life past or present.
Just as scientific discovery is in the soul of the ExoMars programme, Dr Rosalind Franklin knew from a young age that she wanted to be a scientist. Devoted and determined, she followed her dream, graduating with a Natural Sciences degree from Cambridge University, UK, in 1941, and earning a PhD in physical chemistry in 1945. She became an expert in X-ray diffraction imaging, applied to studying the physical chemistry of coals, and later revealing the hidden secrets of DNA, RNA and viruses.
Her legacy lives on today in a number of ways: numerous scientific institutes carry her name – one example being in the Rosalind Franklin University of Medicine and Science in Chicago, U.S, that her niece is a trustee of. Next year her legacy will extend into space, and her adventurous spirit will be lived through the intrepid exploration of the Rosalind Franklin ExoMars rover as it discovers hidden secrets of the Red Planet.
The ExoMars programme is a joint endeavour between ESA and Roscosmos and comprises two missions: the first – the Trace Gas Orbiter – launched in 2016 while the second, comprising the Rosalind Franklin rover and Kazachok surface platform, is planned for 2020. Together they will address the question of whether life has ever existed on Mars. The TGO is already delivering important scientific results and will also relay the data from the ExoMars 2020 mission once it arrives at Mars in March 2021.
Quelle: ESA
----
Update: 27.12.2019
.
Europe's Mars lander passes parachute test
Previous problems appear to have been ironed out in craft’s essential landing equipment
Ground tests designed to validate the deployment of the parachutesthat will be used on the European Space Agency’s (ESA) Mars lander next year have started well at Nasa’s Jet Propulsion Laboratory (JPL) in Pasadena, California. ESA’s ExoMars 2020 mission consists of the UK-built Rosalind Franklin rover, which will look for signs of past or present life, and the Russian Kazachok surface platform, which will monitor the local environment at the landing site.
The parachutes are essential in helping slow down the spacecraft from 21,000km/h at the top of the planet’s thin atmosphere, to virtually nothing six minutes later, when it touches down on the Martian soil. In tests earlier this year, the parachutes sustained damage during deployment. This was traced to the parachute bag in which they were held before being deployed.
Working with Nasa, ESA made modifications to the way the parachutes are released from the bag, which avoids creating so much friction. Using a special rig at JPL, the parachutes have now been tested up to their expected extraction speed of just over 200km/h with no sign of damage. Further confirmatory tests will now take place.
If all goes well, ExoMars 2020 will launch to the red planet sometime between 26 July and 11 August 2020.
Close-up of a test parachute following extraction from its bag. Photograph: Nasa/JPL-Caltech
Quelle: The Guardian
----
Update: 28.12.2019
.
Promising progress for ExoMars parachutes
A series of ground-based tests designed to check the extraction of the ExoMars 2020 mission’s parachutes from their bags have started successfully with promising results to keep the mission on track for next year’s launch.
Landing on Mars is a high-risk endeavour with no room for error. In just six minutes, a descent module with its precious cargo cocooned inside has to slow from around 21 000 km/h at the top of the planet’s atmosphere, to a soft landing at the surface controlled by the lander’s propulsion system.

A key element of reaching the surface safely is based around a parachute system.
For ExoMars 2020, which comprises the Rosalind Franklin rover to explore the planet for signs of life, and the Kazachok surface platform to monitor the local environment at the landing site, a two-parachute system is used, each with its own pilot chute for extraction. The first main parachute has a diameter of 15 m and will be deployed while the descent module is still travelling at supersonic speeds, while the second main parachute has a 35 m diameter, the largest to ever fly on Mars.
Earlier this year, during two high-altitude drop tests, damage to both parachute canopies was observed. Intensive investigations revealed that the main issues concerned the parachute bags, and not the parachutes themselves. Thanks to support from NASA to benefit from their hands-on parachute experience, ESA has made modifications to the way the parachutes are released from the bags, to ease the extraction and avoid frictional damage.

Access the video
The cooperation with NASA has also provided access to special test equipment at NASA’s Jet Propulsion Laboratory that is enabling ESA to conduct multiple dynamic extraction tests on the ground to validate the new design adaptations prior to the upcoming high-altitude drop tests. The ground tests mimic the high speeds at which the parachutes will be pulled from their bags during the descent phase at Mars.
Calibration tests, including low-speed extraction tests at around 120 km/h on both main parachutes and the first high-speed extraction test at a targeted speed of just over 200 km/h on the first main parachute, have already been completed. The low-speed tests were crucial to verify the stability of the new parachute bag design, while the high-speed tests mimic that at which the parachutes will be pulled from their bags during the descent phase at Mars.

Real-time observations of these initial tests showed a clean and correct release of the parachutes from their bags, with no damages seen in either the parachute system or the bag.
“Landing on Mars is difficult and we cannot afford to have any loose ends,” says Thierry Blancquaert, ExoMars Spacecraft Systems Engineering Team Leader. “After many hurdles, the parachute system modifications are moving forward, and these preliminary tests show very promising results that pave the way for the next qualification tests.”
To save time and resources, and to quickly test the proof of concept of the new parachute bags, the initial tests were carried out using the repaired parachutes from the high-altitude drop tests. Given the positive results of the first tests, and following the completion of the high-speed tests, the extractions will be repeated using the existing parachute ‘spares’, which have not been previously damaged or undergone repairs.
Importantly, unlike the high-altitude drop tests which require complex logistics and strict weather conditions, making them difficult to schedule, the ground tests can be repeated on a quick turnaround, buying significantly more time in the test campaign and reducing risk by allowing more tests to be conducted on a short time frame.
Further high-speed tests are planned in the coming weeks to confirm the results of the preliminary tests. Then the parachute systems will be tested again in two high-altitude drop tests in Oregon, US, in February and March 2020. The tests have to be completed prior to the ExoMars project’s ‘qualification and acceptance review’ planned for the end of April in order to meet the 2020 launch window (26 July–11 August).
In the meantime, the rover is nearing completion of its environmental test campaign at Airbus, Toulouse, France. At the same time, the flight model spacecraft that will transport the mission from Earth to Mars, and which contains the carrier module coupled with the Russian descent module, is at Thales Alenia Space, Cannes, France, where it underwent thermal environment tests. The scientific instruments of the surface platform are now being integrated by the Russian Academy of Sciences (IKI). The rover is expected in Cannes in late January, with the integration into the lander foreseen end February.
The mission will launch on a Proton-M rocket with a Breeze-M upper stage from Baikonur, Kazakhstan. Once landed safely in the Oxia Planum region of Mars on 19 March 2021, the rover will drive off the surface platform, seeking out geologically interesting sites to drill below the surface, to determine if life ever existed on our neighbour planet.

All parachute system qualification activities are managed and conducted by a joint team involving the ESA project (supported by Directorate of Technology, Engineering and Quality expertise), TAS-I (prime contractor, in Turin), TAS-F (PAS lead, in Cannes), Vorticity (parachute design and test analysis, in Oxford) and Arescosmo (parachute and bags manufacturing, in Aprilia). NASA/JPL-Caltech has provided engineering consultancy, access to the dynamic extraction test facility, and on-site support. The extraction tests are supported through an engineering support contract with Airborne Systems, who also provide NASA’s Mars 2020 parachutes, and by Free Flight Enterprises for the provision of parachute folding and packing facilities.
The ExoMars programme is a joint endeavour between ESA and Roscosmos. In addition to the 2020 mission, it also includes the Trace Gas Orbiter (TGO) launched in 2016. The TGO is already both delivering important scientific results of its own and relaying data from NASA’s Curiosity Mars rover and InSight lander. It will also relay the data from the ExoMars 2020 mission once it arrives at Mars in March 2021.
Quelle: ESA
----
Update: 17.01.2020
.
'Rosalind Franklin' Mars rover edges closer to launch

Europe's Mars rover, Rosalind Franklin, has just completed a key set of tests ahead of its planned summer launch.
The robot was put in a thermal-vacuum chamber by manufacturer Airbus for several weeks, to simulate the hot and cold conditions it will experience on the way to the Red Planet.
Further evaluations are now planned for the vehicle's various sub-systems.
The European Space Agency rover is scheduled to leave Earth sometime between 26 July and 11 August.
Rosalind Franklin - a joint endeavour with the Russian space agency - is being equipped with instruments to look for signs of present or past life on Mars.
Given the harsh present-day environment on the planet, any biology is most likely to be found underground - and the robot will carry a drill to dig down up to 2m to find the samples for its on-board laboratory to investigate.
- 'Rosalind Franklin' Mars rover assembly completed
- Mars mission test failure threat to launch date
- Can this box answer the biggest question on Mars?
- What chance of finding life on Mars?
Once all the testing is finished at Airbus's factory in Toulouse, France, Rosalind Franklin will be moved to Cannes.
It's in the Mediterranean town that prime contractor Thales Alenia Space (TAS) has one of its main satellite integration facilitates.
TAS will introduce the rover to all the other hardware elements needed for the mission.
These comprise a "cruise stage" stage, an entry capsule and a rocket-powered descent platform.
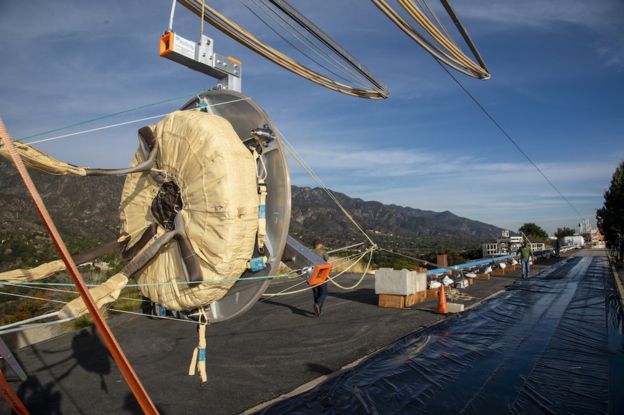
They carry the rover to Mars, protect it during the high-speed atmospheric entry, and, finally, put the robot softly down on the surface of the planet.
All these hardware elements are currently going through their own parallel test phases.
The one issue causing a degree of concern at the moment is the parachute system that will be released at supersonic speeds to slow Rosalind Franklin as it heads down to Mars' surface.
The material in these envelopes was tearing in rehearsals last year.
Esa called in the US space agency (Nasa) to help it get to the bottom of the problem, which seemed to relate to the way the chutes were folded in their containment bags.
ExoMars will have four parachutes. Two main parachutes - at 15m and 35m in diameter - and two much smaller companion drogue chutes.
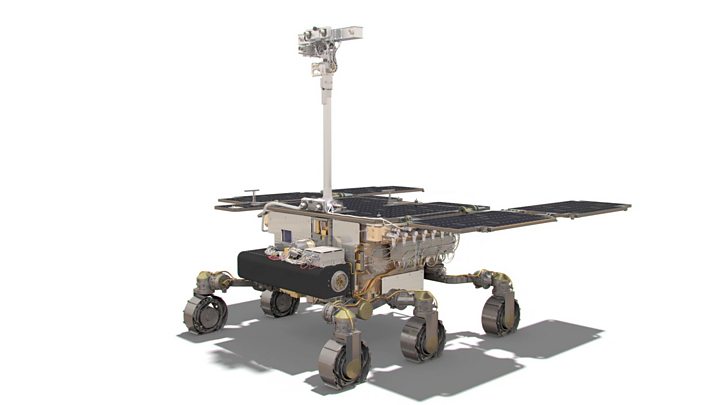
Nasa has been running parachute deployment tests using modified bags. The tests are carried out on a high-velocity wire at the American agency's Jet Propulsion Lab in California.
"We started a sequence of ground tests and we reported publicly before Christmas that the first three were successful," said Dr David Parker, Esa's director of human and robotic exploration.
"I can tell you a fourth test happened on Monday which was the full deployment speed of the large main parachute - so 50m/s deployment of the 35m parachute - and it also was successful.
"We are now shifting our focus to doing two high-altitude drop tests to be carried out in Oregon in the US using the modified bags.
"They're planned for February and March, and only when we've completed those tests will we know that we have a system that's safe to launch."
If the drop tests, which will be conducted from stratospheric balloons, repeat past tearing or show up new problems, the rover mission will have to be postponed.
This would mean a delay of two years. This is the period it takes for Mars and Earth to realign their orbits.
Such a postponement would add cost the project but Esa is not revealing what that would actually entail for commercial reasons. It prefers instead to concentrate on getting the current hardware mission-ready.
"We don't think too much about Plan B because if you do, it's already become Plan A," said Bernardo Patti, a senior official in the human and robotic exploration directorate.
"We are engineering positive. People are working incredibly hard. You should see the commitment," he told BBC News.
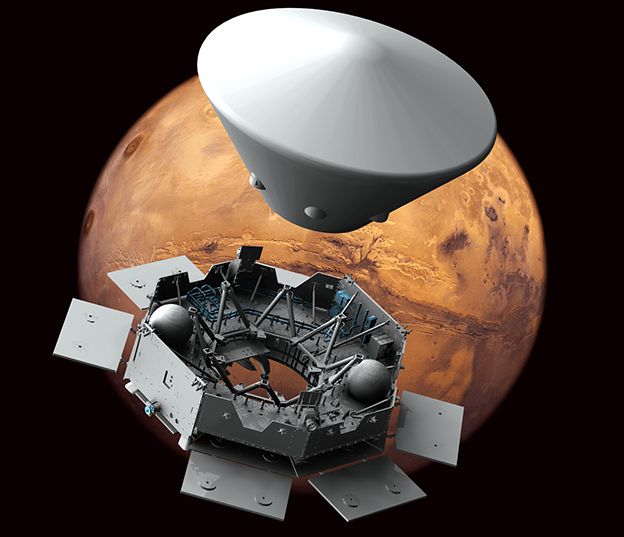
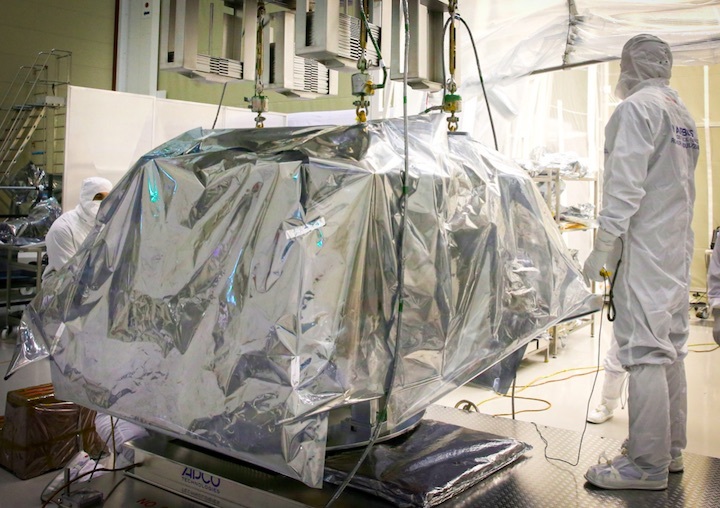
'Rosalind Franklin': Europe's Mars rover heads for fit checks

Europe's Mars rover, "Rosalind Franklin", is on the move again.
The robot has just completed environmental testing at the Airbus factory in Toulouse, France, and is now going east to another aerospace facility run by Thales Alenia Space.
It's on the French Riviera, in Cannes, that the vehicle will join the hardware that will carry it to the Red Planet and put it safely on the surface.
Once this integration is complete, the rover can then go for launch.
Rosalind Franklin is due to leave Earth in July or August this year on a Proton rocket, arriving at Mars in March 2021.
The six-wheeled robot is equipped with scientific instruments designed to look for signs of life.
The project is a joint venture of the European Space Agency (Esa) and its Russian counterpart, Roscosmos.
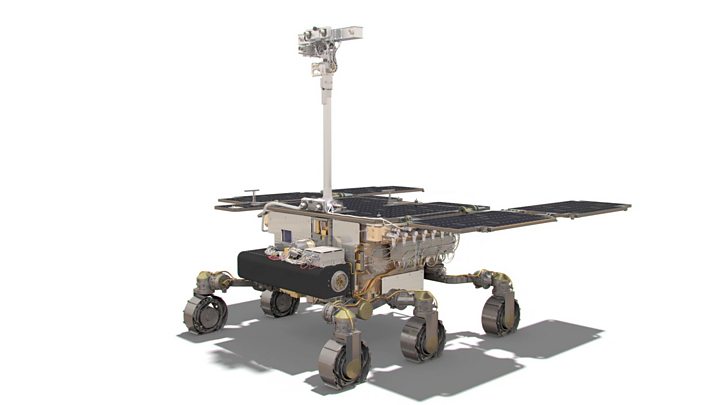
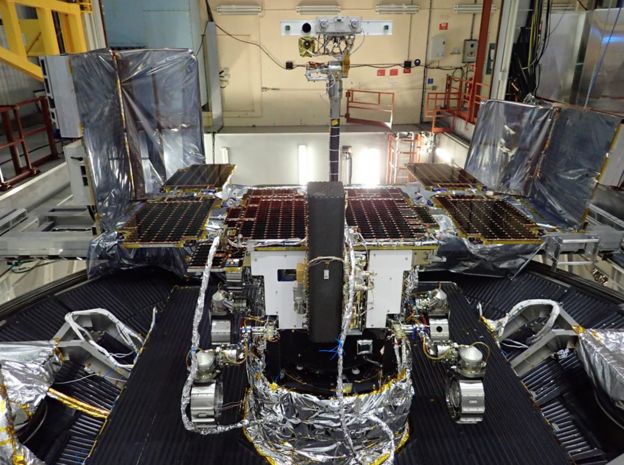

Rosalind Franklin was assembled in the UK over a period of about 18 months. Airbus then took the vehicle to Toulouse to put it in a thermal-vacuum chamber - a testing unit that can simulate the extreme conditions of travelling to, and working on, Mars.
Having survived this challenge of heat, cold and airlessness, the rover must now be joined to its entry, descent and landing (EDL) system; and the spacecraft that will shepherd everything to the Red Planet.
These other elements have been manufactured by different companies across Europe and Russia; and it is the job now of Thales Alenia Space, as prime contractor, to make sure all parts work together.
Assuming no technical problems in this fit-check are encountered, the entire hardware package can move to the Baikonur Cosmodrome in Kazakhstan to meet the launch Proton.
In parallel to all this, Esa continues to work on the parachutes that will help slow Rosalind Franklin during its EDL phase. These chutes, which will be deployed at high velocity, have experienced tearing during testing.
They must perform flawlessly in two final high-altitude practice deployments in the US in the coming weeks before the final go-ahead for the rover mission is given.
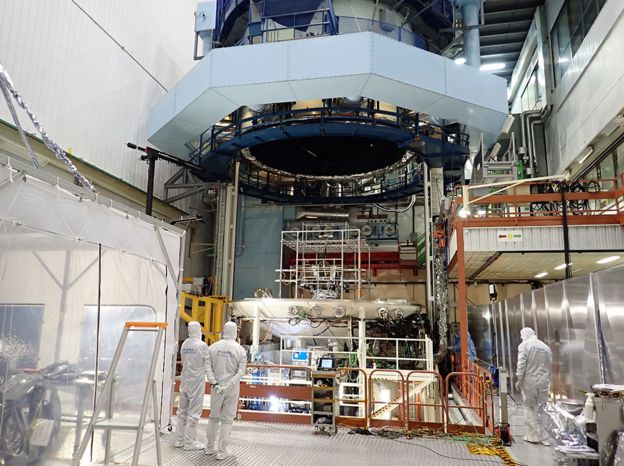

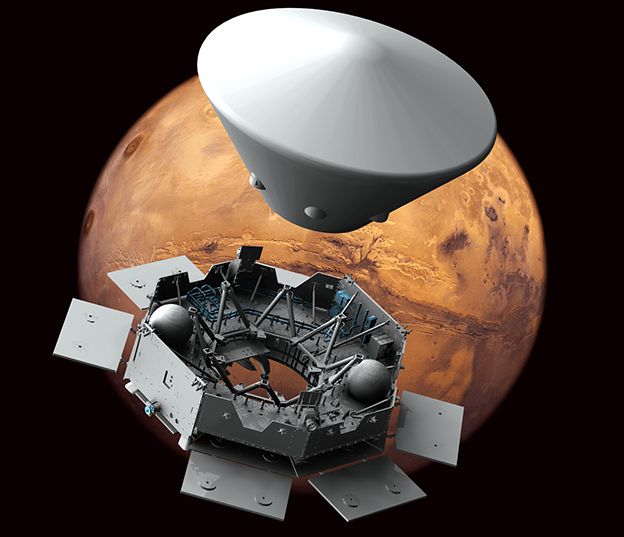

Quelle: BBC
----
Update: 27.02.2020
.
Delay seems likely as parachute problems plague European Mars lander
"This plan will be examined by the two agency heads."
The European and Russian space agencies have announced they will decide the fate of their ExoMars mission at a meeting on March 12.
The joint mission to deliver a rover and suite of scientific instruments to the surface of the red planet is set for a July on a Proton rocket from the Baikonur Cosmodrome in Kazakhstan. However, serious questions were raised about the viability of the lander's complicated parachute systems last year and ongoing problems in testing them.
According to a spokesperson for the European Space Agency (ESA), a "working-level review" for the project was held among ESA and Roscosmos officials in late January, and a preliminary assessment was forwarded to the respective heads of the space agencies, Jan Wörner of ESA and Dmitry Rogozin of Roscosmos, on February 3.
"They instructed the respective inspectors general and program chiefs to submit an updated plan and schedule covering all the remaining activities necessary for an authorization to launch," the ESA spokesperson said. "This plan will be examined by the two agency heads who will meet on 12 March to jointly agree the next steps."
It appears that the European and Russian officials will make a public announcement about ExoMars next month. Their options include pressing ahead with a launch this year or delaying two years until the next favorable window for a launch to Mars opens. Given multiple issues with the mission, a source said a delay is the most likely option.
Parachutes
ExoMars has a two-part system of parachutes to safely bring its the European-built Rosalind Franklin rover and the Russian-led surface platform, Kazachok, to the surface. The first pilot parachute and a 15-meter main parachute are deployed while the lander is still traveling at supersonic speeds through the thin, upper Martian atmosphere. The second set of pilot and main parachutes, which are larger, are deployed at subsonic speeds.
In May 2019, damage occurred to both main parachute canopies during a high altitude drop test from 29km. After assessing the problem and making changes to the design of the parachutes and their bags, the agency conducted another high-altitude test on August 5, this time focusing solely on the larger canopy that deploys in the lower atmosphere. This test, too, was not successful.
The mission has yet to complete a successful high-altitude test of its parachute system and was planning to work with NASA's Jet Propulsion Laboratory in February to complete such a trial. Despite promising results from ground-based tests, Russian media reports that that high-altitude tests have now been delayed from February to March.
Rover “pit stop”
Meanwhile, Thales Alenia Space has discovered a defect in the hinge system for the rover's upper-level solar arrays, the BBC reports. The issue was found in both the rover test model and the actual flight model during the process of thermal vacuum chamber testing. Glue that held the brackets in place came unstuck. Engineers are developing a fix.
It is no easy thing to reach Mars. No space agency other than NASA has ever successfully soft landed and operated spacecraft on Mars for longer than a few seconds. In October 2016, the European Space Agency failed to successfully land its Schiaparelli lander after the spacecraft jettisoned its parachute earlier than expected.
This will be a busy year for Mars launches. NASA's Mars 2020 rover is due to launch in July, and with its HX-1 mission, China plans to launch an orbiter, lander, and rover all in one package. Finally, the United Arab Emirates will attempt to fly its Hope Mars Mission orbiter during the July window. The orbiter will launch from Japan on an H2-A rocket.
Quelle: arsTechnica
+++
Europe's Rosalind Franklin Mars rover to make 'pit stop' for repair
Europe's Mars rover will have to make a "pit stop" for a minor repair when it is moved from France to Italy.
The vehicle, which is currently undergoing final preparations in Cannes prior to a summer launch, has developed a small problem with its solar panels.
Glue that holds brackets in place on the folding arrays has come unstuck.
It's not considered a serious problem and will be fixed when the "Rosalind Franklin" robot passes through Turin on its way to the launch site.
Rosalind Franklin, also known by its codename ExoMars, is a joint venture of the European and Russian space agencies (Esa and Roscosmos).

Various companies and institutions have been contracted to contribute pieces of hardware under the leadership of the Franco-Italian aerospace outfit Thales Alenia Space.
It is TAS that will be moving the rover from its Cannes factory to one in Turin before shipping out to the launch complex at Baikonur in Kazakhstan. The robot is due to arrive at the famous spaceport in mid-May.
The glue defect has occurred in the hinge system on the top-deck solar arrays; specifically, in the brackets that hold and fold the outer wings for the journey to Mars.
The issue was noticed in both the rover test model and the "flight model" (the version of robot that actually goes to Mars) after they emerged from thermal-vacuum testing.
This is the process in which hardware is put in a chamber and confronted with the kinds of swings in temperature it will likely experience during a space mission.
The fix will now involve putting bolts through the brackets to make sure the solar panel wings are securely fastened. Rosalind Franklin is well within its mass target, so engineers are unconcerned about resorting to a heavier solution than glue.
Although not a major issue, this is a glitch the project could have done without.
Officials are in the process of trying to corral the final phases of preparation against the background of a ticking clock.
Opportunities to go to Mars come around only once every 26 months when the planets are favourably aligned. This means Rosalind Franklin has to leave Earth in a narrow window in July/August this summer or skip to the next launch possibility in 2022.
The heads of the agencies, Esa's Jan Wörner and Roscosmos's Dmitry Rogozin, announced on Monday that they would hold a joint press conference in Moscow on 12 March to give a status update.
All the hardware required to send Rosalind Franklin to Mars and land it gently on the surface is built, but there is still a long list of checks that need to be gone through before anything can be put atop a rocket.
This list includes some final stand-out tests on the parachutes and the retro-rockets that will lower the robot to its touchdown location on the Oxia plain at Mars' equator.
There is also the general compatibility and fit-checks of the various elements that will comprise what some describe as the "Russian doll" stack.
This refers to the rover and its landing platform, which together fit inside a capsule, which is then attached to a "cruise stage" - the spacecraft that shepherds everything to the Red Planet.
To give one example of the checks that must be completed: the cruise stage spins for stability in flight. The rover and platform inside their capsule therefore have to be balanced carefully, just like a car tyre, to ensure there is no disruptive wobble.
If all goes to plan, Rosalind Franklin should land on the Red Planet in March 2021. It is being equipped with instruments and a drill to search for signs of life - in the present day or in the distant past.
It is one of four Mars missions targeting the July/August launch window. The others are being prepared in the US, the UAE and China.
Quelle: BBC
----
Update: 3.03.2020
.
ExoMars parachute tests delayed, mission faces review
HELSINKI — The European and Russian space agencies have delayed crucial ExoMars 2020 parachute tests to late March, with the mission also set to face review.
“The high altitude drop tests of the two main parachutes are now planned for the end of March 2020,” an ESA spokesperson told SpaceNews via email.
The tests of the 15-meter-diameter supersonic and 35-meter-wide subsonic parachutes—an essential part of the entry, descent and landing phase of the mission—had been scheduled for December and February.
The delay comes despite six ground tests demonstrating successful parachute extraction – the point at which damage was caused in earlier, failed high altitude tests.
Both tests need to be successful for the go-ahead for launch of 300-kilogram Rosalind Franklin rover during the July 25 to Aug. 13 Mars launch window. Any failure would mean a wait of 26 months for the next launch window, opening late 2022.
Agency heads to decide next steps
However the ExoMars mission could be condemned to delay before the tests are even carried out. The heads of ESA and Russian partner Roscosmos are set to meet next week to discuss next steps following a report on the progress of the mission.
A working-level review of the ExoMars 2020 project held late January, with a preliminary assessment communicated to the heads of the two space agencies on 3 February.
In response, ESA’s Jan Woerner and Dmitry Rogozin of Roscosmos “instructed the respective inspectors general and program chiefs to submit an updated plan and schedule covering all the remaining activities necessary for an authorization to launch,” the ESA spokesperson stated.
“This plan will be examined by the two agency heads who will meet on 12 March to jointly agree the next steps.”
The decision will be announced at a press briefing held afterwards in Moscow shown live on ESA Web TV.
The ExoMars 2020 mission still faces a final review scheduled April 2020. Parachute issues and any other problems will need to have been solved by this point.
An issue with the rover Rosalind Franklin rover itself will need to be remedied, though this is not thought to be a major issue.
“There is a minor de-bonding of part of the solar array following the system environmental tests. This is a repeat of a problem seen during some earlier tests and a mechanical fix has been foreseen and will be implemented at TAS-I (Torino),” the ESA spokesperson said. “It is not seen as a serious problem.”
ExoMars Parachute tests unfold
A Russian Proton rocket is planned to launch ExoMars rover in July, reaching Mars in March 2021. It will employ a complex system of four parachutes, with two small pilot chutes used to sequentially deploy the supersonic ‘disc–gap band’ chute and subsonic main chute.
High altitude drop tests of the 15-meter-diameter supersonic and 35-meter-wide subsonic parachutes failed in August and May 2019, threatening delay.
ESA turned to NASA’s Jet Propulsion Laboratory for assistance, with inspectors finding that damage to the chutes was caused at the point of extraction from their bags. “The focus is on adapting and simplifying the bag [rather] than touching the parachutes,” Francois Spoto, ExoMars program manager, told SpaceNews in September.
The new high altitude drop tests will be carried out in Oregon in the United States. The Esrange Space Center, northern Sweden, hosted the earlier tests.
The unprecedented size and complexity of the parachute system is related to the lander provided by Roscosmos. A more powerful retropropulsive system on the lander could have allowed the mission to require only one main chute, according to Spoto.
ESA and Russia failed to land on Mars with its joint ExoMars 2016 Schiaparelli demonstration lander. A computer issue led to the premature release of its parachute and brief firing of braking thrusters.
NASA, China and the United Arab Emirates are also planning to launch to the Red Planet in July and August.
Quelle: SN
----
Update: 4.03.2020
.
Russia completes firing tests of propulsion unit for ExoMars lander
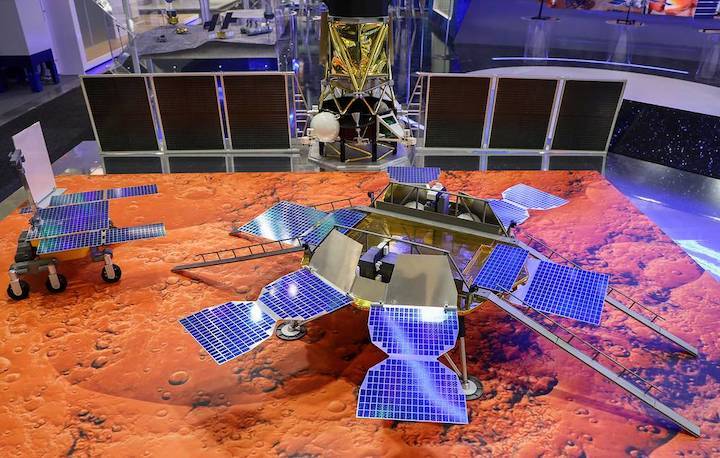
"As part of implementing the ExoMars international project, the firing tests of the propulsion unit of the ExoMars spacecraft’s lander were completed on February 27, 2020," the statement runs.
According to the preliminary analysis, the assignments were fulfilled with positive results, the Lavochkin press office reported.
ExoMars is a joint program of the European Space Agency and Russia’s Roscosmos federal space agency to study Mars. The mission will be launched in July-August 2020 by a Proton-M carrier rocket with a Briz-M booster from the Baikonur Cosmodrome. The project aims to study the Martian surface, its atmosphere and climate.
Quelle: TASS
----
Update: 13.03.2020
.
Europe, Russia postpone joint rover mission to Mars
The European Space Agency and Russia's Roscosmos are postponing a planned joint mission to Mars until 2022, in part due to travel restrictions resulting from the new coronavirus outbreak
BERLIN -- The European Space Agency and Russia's Roscosmos said Thursday they are postponing a planned joint mission to Mars until 2022, in part due to travel restrictions resulting from the new coronavirus outbreak
The ExoMars mission was due to launch this year but concerns about possible technical problems had already prompted both agencies to discuss the delay.
“We want to make ourselves 100% sure of a successful mission,” European Space Agency Director General Jan Woerner said in a statement. ”We cannot allow ourselves any margin of error. More verification activities will ensure a safe trip and the best scientific results on Mars."
Dmitry Rogozin, the head of Roscosmos, said the delay was primarily due to technical problems, compounded by the coronavirus outbreak, "which left our experts practically no possibility to proceed with travels to partner industries.”
The mission's goal is to put a rover on the red planet to help determine whether there has ever been life on Mars. Scientists hope the rover, packed with high-tech instruments and named after British chemist Rosalind Franklin, will be able to dig for biological signatures of life below the martian surface and also provide further insights into the planet's history of water.
The postponement is another setback for the ExoMars program after the 2016 launch of an orbiter and a test lander. The Trace Gas Orbiter was successfully deployed, but the Schiaparelli lander malfunctioned and crashed on the surface of Mars, highlighting the difficulty of putting a probe on the planet.
So far, the United States is the only country to successfully land a functioning probe on Mars. NASA's Curiosity and InSight landers are still in operation on the planet.
Three other Mars missions are planned for this summer. The United States is launching a lander, China has a lander-orbiter combo, and the United Arab Emirates is sending an orbiter.
Spacecraft can only be launched to Mars every two years, to take advantage of the best possible lineup between Earth and its neighboring planet.
NASA’s science mission chief, Thomas Zurbuchen, said ESA and Roscosmos made a “tough decision” in delaying the ExoMars mission.
“Launching & safely landing a spacecraft on Mars are extremely demanding and require many technologies & systems to function perfectly,” he wrote on Twitter.