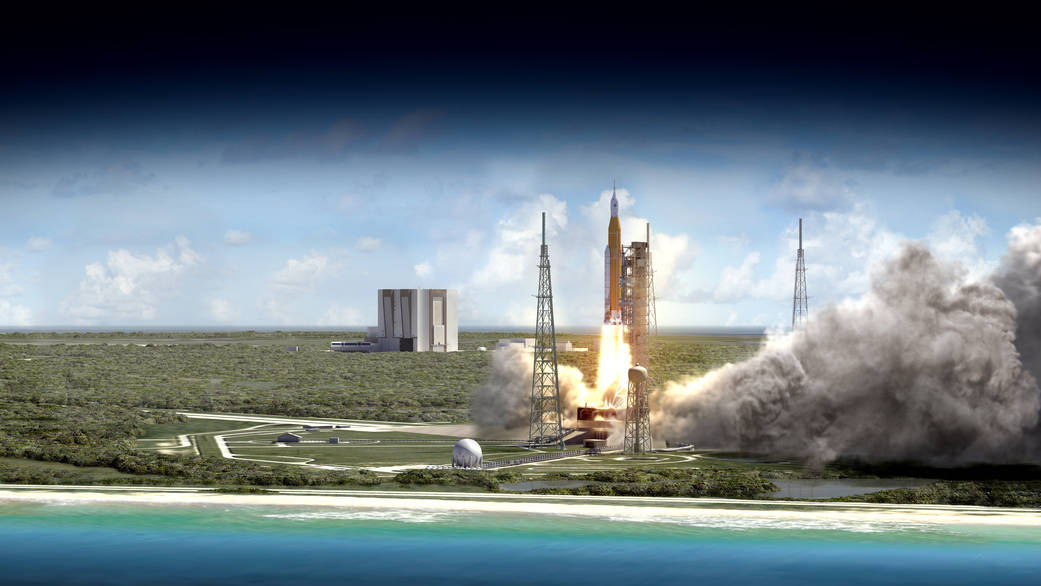
An SLS Block 1 launch vehicle hoists an Orion spacecraft from KSC’s Pad 39B, with the VAB in the distance. Image Credit: NASA/MSFC
It seems as if we’re galloping toward the end of 2016, and we’re getting closer by the day to the “dawn” of a new U.S. launch vehicle and human-rated spacecraft. In a little over two years, NASA’s next “giant leap”—Exploration Mission 1 (EM1)—is aimed for a launch from Kennedy Space Center’s (KSC) Pad 39B. While two years may seem like a long time, much must take place before the Space Launch System (SLS) launch vehicle and its Orion crew capsule (integrated with a European Space Agency-built service module) are ready to leave Earth’s orbit for a flight 40,000 miles beyond the Moon and back.
On the SLS front, NASA continues to prepare KSC’s Vehicle Assembly Building (VAB) for the next-generation launch vehicle, while the massive core stage comes together at the space agency’s Michoud Assembly Facility in New Orleans, La. Meanwhile, the Orion crew capsule to be used for EM-1 received its essential heat shield. NASA is also preparing to test the ESA-built service module, and recovery processes after splashdown are also being practiced at Houston’s Johnson Space Center.
VAB Receives Modifications for SLS, While Core Stage Comes Together at Michoud
KSC’s iconic Vehicle Assembly Building (VAB), which was built during the mid-1960s for Apollo lunar missions, also supported the Skylab and shuttle programs. As we approach the 2020s, it now is en route to supporting SLS/Orion. NASA announced that the second half of the “D” level work platforms (D north) for the SLS launch vehicle were installed by a heavy-lift crane inside High Bay 3 of the VAB on Sept. 9. These platforms are the seventh of 10 levels of work platforms meant to provide machinery and workers with access to the heavy-lift rocket prior to EM-1. NASA stated that these modifications have been overseen by the Ground Systems Development and Operations Program. The SLS modifications to the VAB are now well over halfway complete.
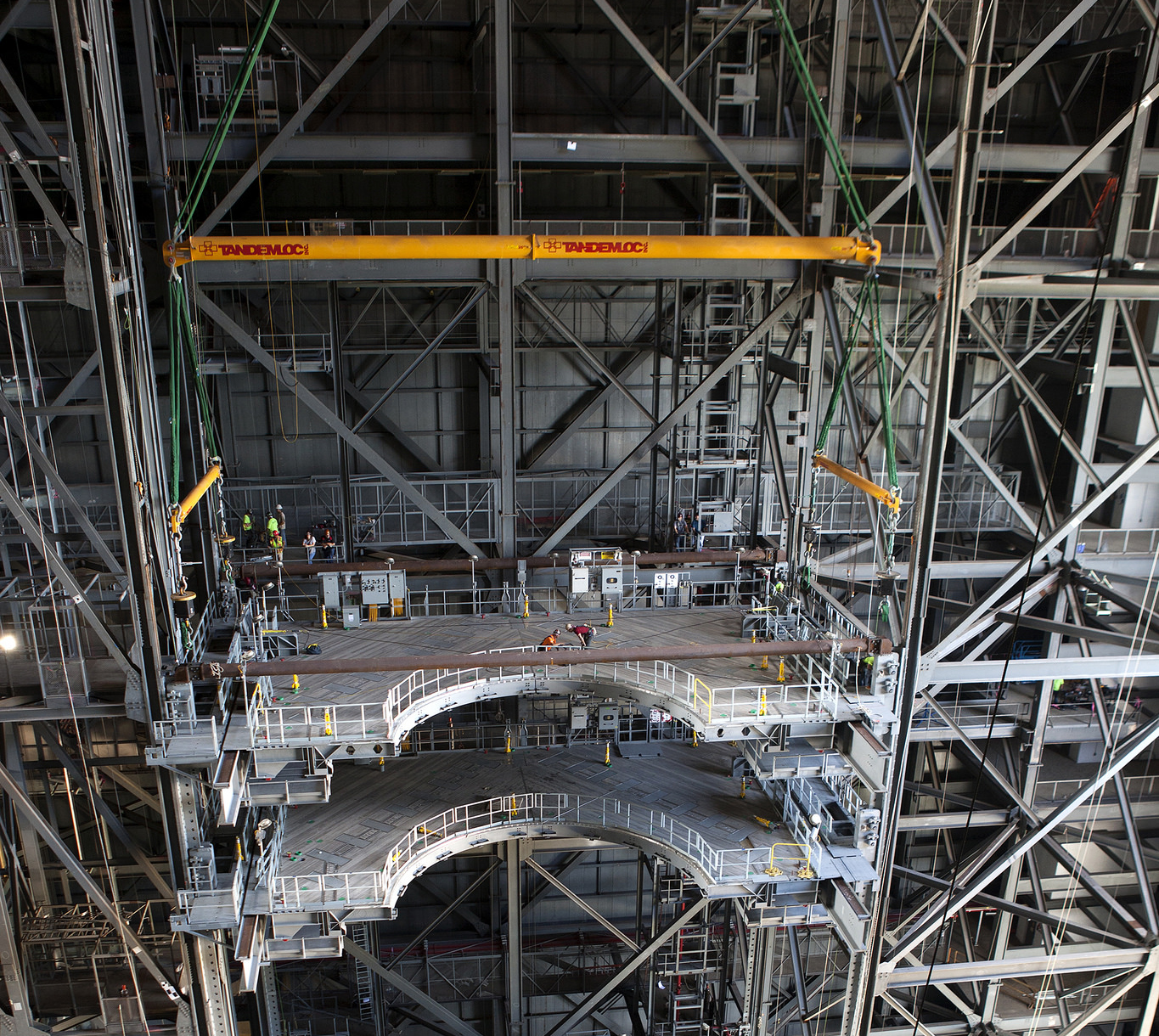
From NASA: “A heavy-lift crane lowers the second half of the D-level work platforms, D north, for NASA’s Space Launch System (SLS) rocket, into position Sept. 9 for installation in High Bay 3 in the Vehicle Assembly Building at the agency’s Kennedy Space Center in Florida.” Photo Credit: NASA/Ben Smegelsky
It was also announced that welding was completed on the 130-foot-tall liquid hydrogen tank that will be utilized for EM-1 in late 2018. At present time, the rocket’s 212-foot-tall core stage is meticulously being put together by engineers at NASA’s Michoud Assembly Facility. NASA stated that at the facility’s Vertical Assembly Center, many of the core stage’s elements are being welded. In addition to the large hydrogen tank, the forward skirt, liquid oxygen tank, and engine section are also being welded at Michoud; another component, the intertank, is being fabricated there as well. The Boeing Company is the core stage’s prime contractor.
The SLS’s mammoth core stage will carry 2.3 million pounds of liquid hydrogen and liquid oxygen, which will in turn fuel four RS-25 engines, the same type of engine that powered the space shuttles reliably for 30 years. Together, this combination makes for a lot of power, and a lot of stresses.
To make sure they can take the pressure, the “wet” fuel-bearing sections of the rocket will undergo rigorous tests (such as hydrostatic and pneumatic testing) to be proven flight ready. “Dry” structures (such as avionics, cameras, computers, and assorted electronics) will be added, along with all-important orange-colored insulation so the rocket can withstand the extreme cold of liquid fuel temperatures, and the intense heat of launch. Joan Funk, SLS core stage lead at NASA’s Marshall Space Flight Center in Huntsville, Ala., likened the process to “building a house.” She related, “With the massive, welded elements coming off the Vertical Assembly Center at Michoud, we’ve laid the foundation, framed the walls and put up the roof. The big items are in place. Now it’s time to get to work on the inside.”
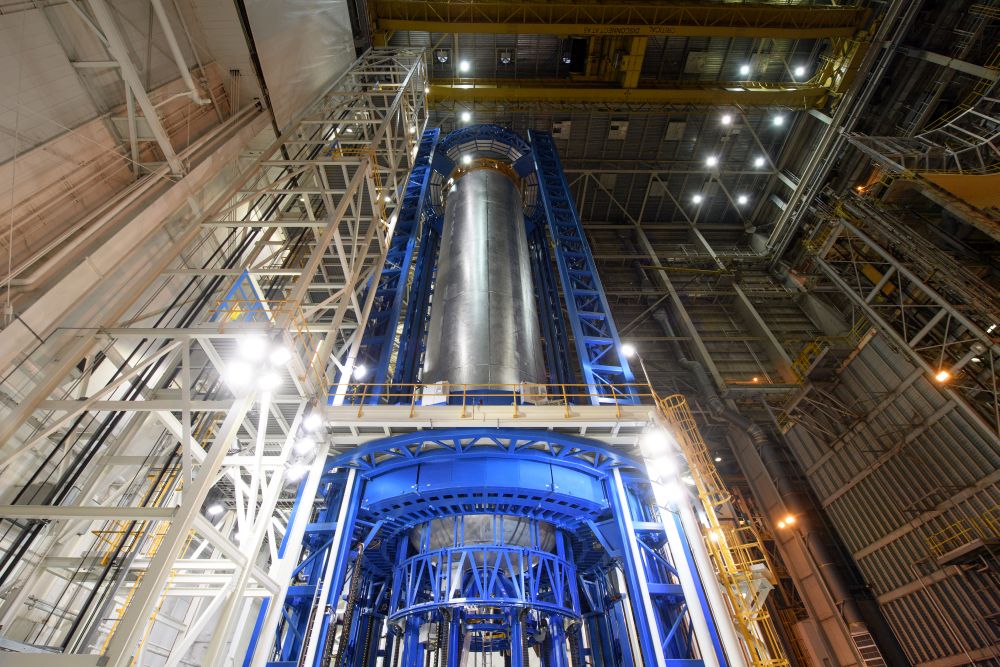
From NASA: “Engineers just completed welding the liquid hydrogen tank that will provide fuel for the first SLS flight in 2018. The tank measures more than 130 feet tall, comprises almost two-thirds of the core stage and holds 537,000 gallons of liquid hydrogen — which is cooled to minus 423 degrees Fahrenheit.” Photo Credit: NASA/Michoud/Eric Bordelon
Following work at Michoud, the core stage will travel by barge to NASA’s Stennis Space Center in Mississippi for further testing and a hot fire test called a “green run,” in which the rocket’s engines are fired at nearly full power attached to the core stage. Once these milestones are completed, the core stage will head to KSC’s newly-modified VAB for its maiden voyage. The next destination? Into space.
Orion Update: Heat Shield, ESA’s Service Module, and Recovery Tests
While SLS continues to take shape, the Orion crew capsule to be used for EM-1 received a special delivery in August: its essential heat shield, which was transported via NASA’s Super Guppy aircraft to KSC’s Shuttle Landing Facility (SLF). Following its arrival, the still-boxed shield was taken to the Neil Armstrong Operations and Checkout (O&C) Building at the space center, where it was uncrated and placed on a stand. The 16.4-foot-wide heat shield was built by Lockheed Martin, Orion’s prime contractor, and the NASA Orion team at the company’s facility in Denver, Colo.
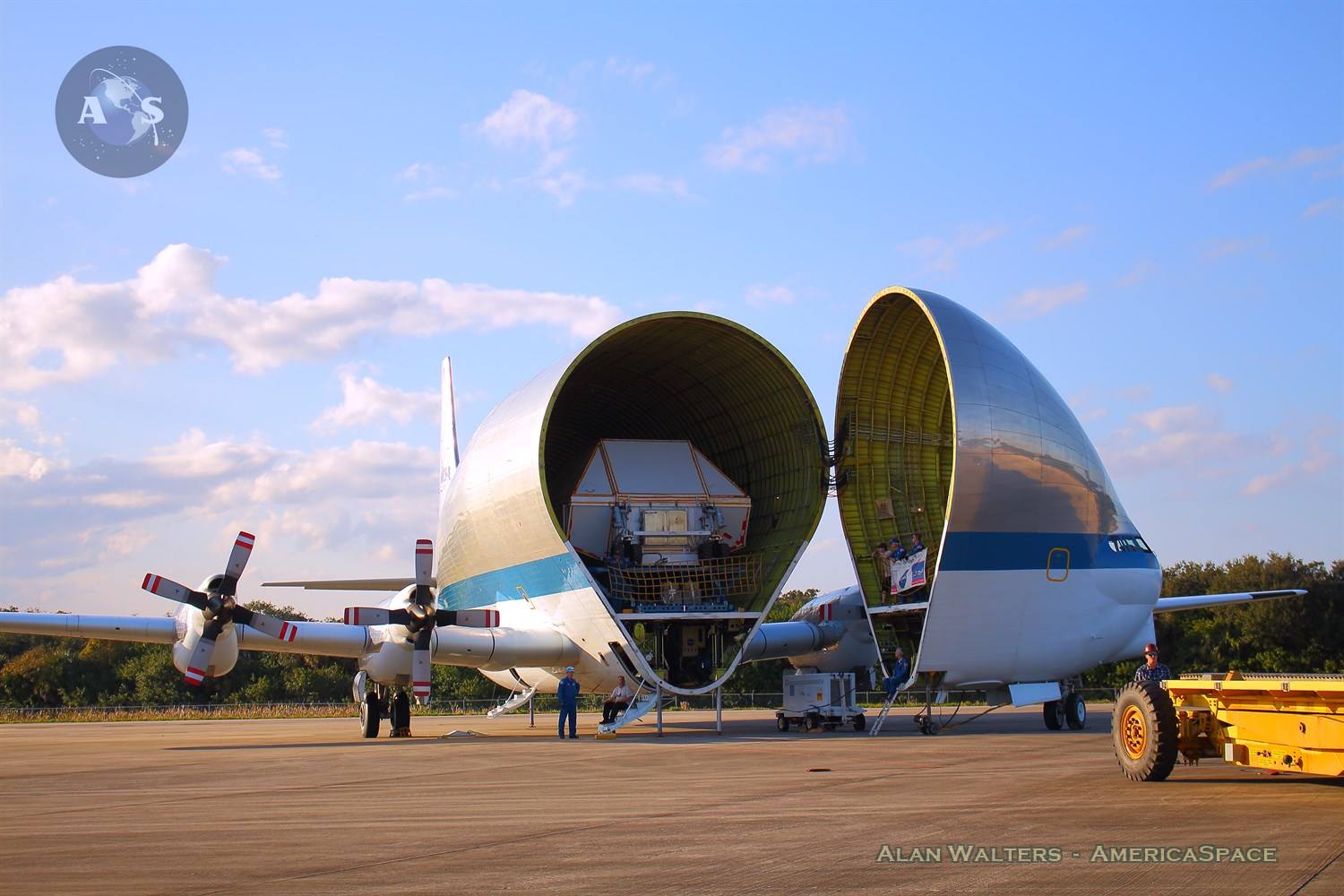
The structure of the first Orion spacecraft destined to fly atop NASA’s Space Launch System (SLS) rocket in late 2018 on Exploration Mission-1 (EM-1) arrived at the agency’s Kennedy Space Center (KSC) in Florida Feb. 1, 2016. Photo Credit: Alan Walters / AmericaSpace
NASA stated that the heat shield for EM-1 will have some differences from the one flown on EFT-1, Orion’s first test flight, which took place in December 2014 aboard a United Launch Alliance Delta IV Heavy launch vehicle. The space agency emphasized that this time around, blocks of Avcoat (an ablative thermal substance) will be bonded to the shield; during EFT-1, the substance was filled into honeycomb cell structures. Of course, instrumentation will be attached to the spacecraft to give engineers an idea of how the heat shield responds to a high-energy reentry coming back from a deep space destination.
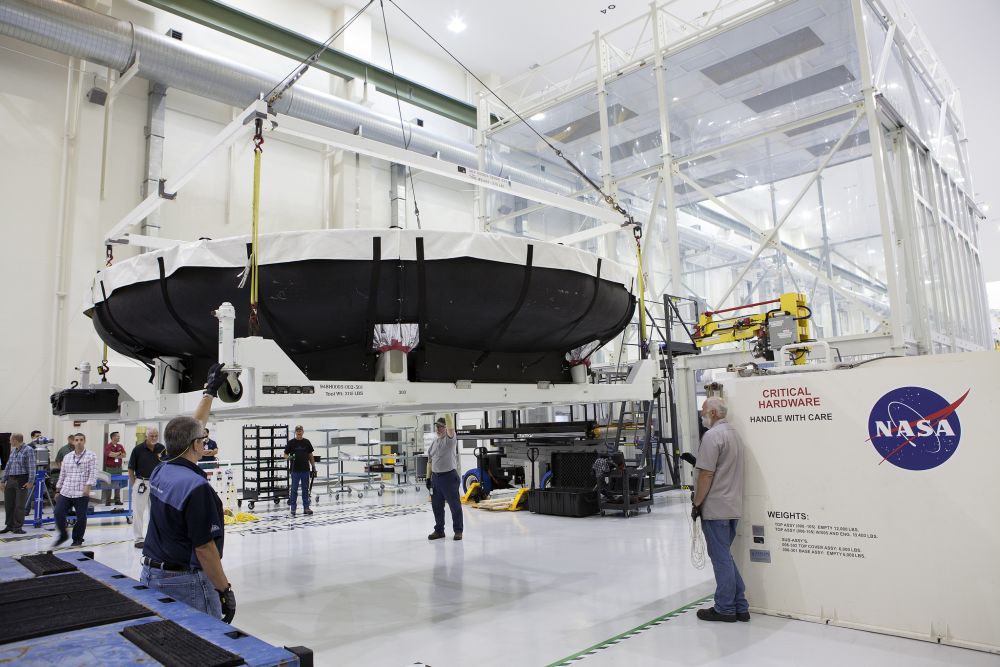
From NASA: “Inside the Neil Armstrong Operations and Checkout Building high bay at NASA’s Kennedy Space Center in Florida, technicians assist as a crane lifts the Orion heat shield for Exploration Mission 1 away from the base of its shipping container. The heat shield arrived aboard the agency’s Super Guppy aircraft at the Shuttle Landing Facility, managed and operated by Space Florida, from Lockheed Martin’s manufacturing facility near Denver. The Orion spacecraft will launch atop NASA’s Space Launch System rocket on EM-1, an uncrewed test flight, in 2018.” Photo Credit: Photo credit: NASA/Dimitri Gerondidakis
NASA also stated that in spring 2017, propulsion qualification testing for Orion’s European Service Module will take place at its White Sands Test Facility in Las Cruces, N.M. According to the space agency, the propulsion qualification module to be tested contains “flight-like test units of the engine, propellant systems, and propulsion control units.” The module is currently being built by ESA’s contractor, Airbus Defence and Space.
Another important facet of the Orion program involves recovery. For the first time since the mid-1970s, humans will splashdown under parachutes in the ocean following space missions. This is a far cry from the shuttle days, when crews could merely walk down a flight of stairs following a spaceflight. To be prepared, NASA is already practicing at-sea recovery operations. On Wednesday, Sept. 21, a group of U.S. Navy divers, Coast Guard rescue swimmers, and U.S. Air Force pararescuemen utilized an Orion capsule mockup for practice purposes at Johnson Space Center’s Neutral Buoyancy Laboratory in Houston.
*****
While the VAB modifications and the SLS core stage continue to come together, the Orion crew capsule also is meeting vital milestones in order to make its next journey. EM-1, currently scheduled to launch in October 2018, will see the Orion crew capsule integrated with its European Service Module making a flight aboard a Block I SLS launch vehicle. Its next journey will take it well beyond the Moon and back, exposing the spacecraft and heat shield to high forces and temperatures (of up to approximately 5,000 degrees Fahrenheit). This mission will be another crucial stepping stone as NASA prepares to send humans further into deep space than ever before, to destinations such as Mars, our closest planetary neighbor.

From ESA: “Proposal for a Multi-Purpose Crew Vehicle-Service Module (MPCV-SM).” Orion’s European service module will fly on Exploration Mission-1 (EM-1) in late 2018. Image Credit: ESA-D. Ducros
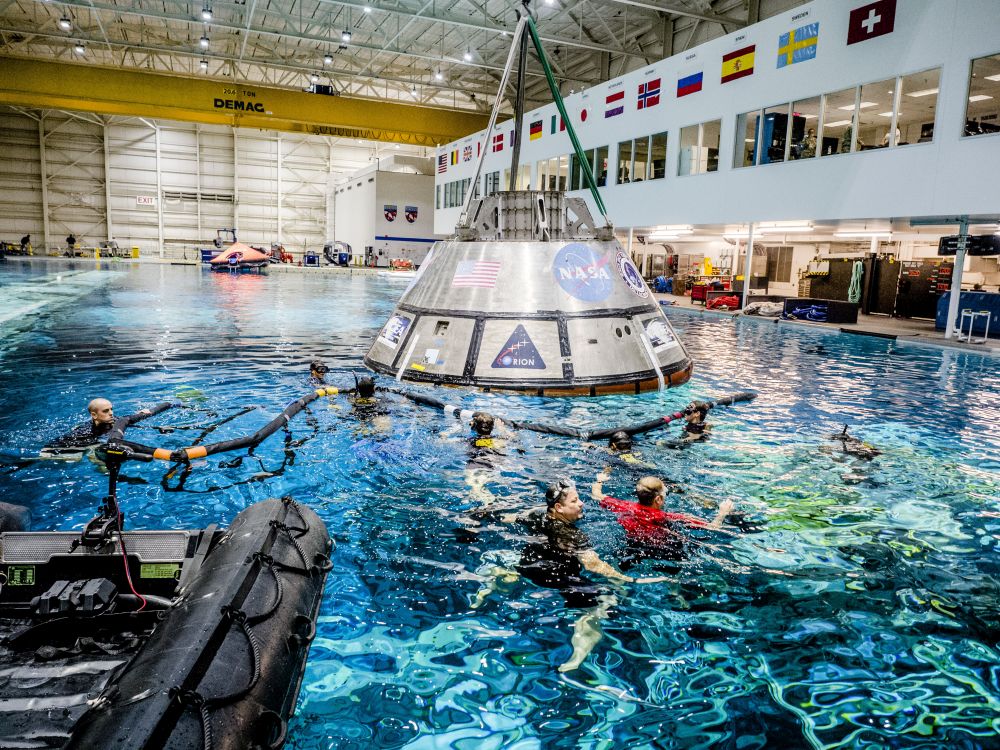
From NASA: “A group of U.S. Navy divers, Air Force pararescuemen and Coast Guard rescue swimmers practice Orion underway recovery techniques in the Neutral Buoyancy Laboratory at NASA’s Johnson Space Center in Houston on Sept. 21, 2016.” Photo Credit: NASA/Radislav Sinyak
Quelle: AS
-
Update: 29.09.2016
-
Orbital ATK prepares for final casting of SLS EM-1 flight SRBs
Following the highly successful test firing of the Qualification Motor 2 (QM-2) at their proving grounds near Promontory, Utah, Orbital ATK is preparing for the second half of casting operations for the Solid Rocket Booster segments that will power the SLS EM-1 mission through the first two minutes of flight – while at the same time working through a minor issue that is not expected to affect SLS SRB production timelines.
QM-2: success for cold temp firing of SRB:
QM-2 was the second in a two part qualification firing program for the new five-segment SRBs to validate the final configurations, manufacturing processes, propellant design, and operational temperature range for the propulsion element that will provide 86.74% of SLS’s thrust at liftoff.
The first qualification test, QM-1, validated all of these elements in the high-end of the SRB certified operational temperature range; QM-2tested the low-end temperature range.
While the SRB high-end temperature range never caused a delay or concern for delay during the Shuttle program, the low-end temperature range became a major consideration for flight operations in 1985.
During the 24 January 1985 launch of Shuttle Discovery on STS-51C, liftoff occurred with an ambient air temperature of 53°F – having risen to that from a lower temperature in the preceding overnight hours.
Post-flight recovery and inspection of the STS-51C SRBs revealed charring to the primary O-rings on both SRBs as well as a burn through penetration of the primary O-ring on the center field joint of the right SRB and heavy charring on the secondary O-ring – indicating a near burn through event of the field joint.
Despite this revelation to Morton Thiokol (predecessor to ATK), the reality of minimum operational temperature limits for SRB certified use was not readily understood by everyone one year and four days later.
On 28 January 1986, with a predicted air temperature of just 34°F at the 09:36 EST targeted launch time of STS-51L, Challenger was approved for launch by NASA and Morton Thiokol managers over what, at the time, were unknown to NASA objections from Thiokol engineers due specifically to the hard freeze temperatures reached at the pad in the overnight hours.
During the Rogers’ Commission hearings into the loss of Challenger, several Thiokol officials’ testimonies revealed seemingly conflicting understandings on the minimal safe operational temperatures for the SRBs.
A key element revealed at the hearings were that some engineers thought 53°F was cold enough to be problematic while others thought the temperature had to be much lower – at 40°F.
Other testimony complicating understanding of the minimal safe temperatures for the SRBs revolved around whether that 40°F lower limit was air temperature or propellant mean bulk temperature – a significant difference given that the mean bulk propellant temperature for Challenger’s SRBs was calculated to be above both the 40°F and 53°F limits discussed.
Regardless, safety improvements, joint heaters, and a structured minimum allowable air temperature for launch chart was created in the wake of Challenger and adhered to for the duration of the program.
Since 1986, Thiokol – which became ATK and now Orbital ATK – has maintained a dedication to understanding how the SRBs operate in their lower and maximum temperature ranges.
For QM-2, which was fired on 28 June 2016, Jeff Foote, Orbital ATK Vice President of NASA Programs, noted that “QM-2 was a very clean and highly successful test firing. Instrumentation data yield was extremely good, and included some instrumentation that will fly on EM-1.”
At this time, all major disassembly operations of the QM-2 motor have been completed, and Orbital ATK’s teams are continuing to dissect components and make standard measurements in the nozzle and case insulation.
Of particular note, the redesigned nozzle joint 1 performance was “excellent”, and Orbital ATK was able to use QM-2 to gather “valuable dynamics data” on the Aft Booster Separation Motors (BSM) and housing – the first time such data has been gathered on a five segment SRB.
SLS EM-1 booster casting operations:
As with most things in spaceflight, operations usually parallel and overlap with one another.
This was certainly the case with the QM-2 static fire in June and the commencement of casting operations for the flight set SRBs that will propel the EM-1 mission skyward in 2018.
As of this month, Orbital ATK has completed casting of five of the 10 booster segments for the SLS EM-1 mission.
In casting order, Orbital ATK currently has the Left Hand (LH) aft segment, the Right Hand (RH) center/forward segment, LH center/forward, LH forward, and RH aft segments cast.
However, casting operations are currently on hold pending the outcome of an investigation into cracking of a thin adhesive layer within the insulation that was discovered during routine testing of samples that were not taken from the already cast EM-1 segments.
Orbital ATK elaborated on this point to NASASpaceflight.com, stating that “There has been no cracking of any material within the propellant/liner/insulation system in the inspected EM-1 segments and QM segments that have been dissected.
“The question has to do with a thin adhesive layer within the insulation and whether stresses under long-term storage conditions challenge structural margins in very specific regions of some segments.
Mr Foote elaborated, stating that “Over the summer, some insulation samples were tested for the purpose of overall design certification analysis.
“The samples revealed the possibility of some brittle behavior in the adhesive layer under specific test conditions that are outside of normal vehicle operating parameters.
“Until that possibility is fully assessed, a minor change was made to alleviate the concern in certain areas of the segment insulation and that will cause a short schedule pause in segment casting in order to implement.”
At this time, casting is set to resume in early November with the RH forward segment.
This will then be followed by casting of the two center segments, before moving on to cast the RH center/aft, and the LH center/aft segments.
Of note, this minor delay to casting is not expected to have any impact on the overall EM-1 SRB production timeline.
After casting operations are complete, the segments will undergo standard post-casting inspections and verifications before entering final production facility processing in 2017.
Of the five segments already cast, all five of them have “passed through NDT (x-ray) inspection”, notes Mr. Foote.
Under the current production schedule, all 10 segments will be ready for delivery to KSC in September 2017.
As with Shuttle, the SRB segments will make their way across the U.S. via railcar – using the same cars that were used to transport all of the Shuttle SRB segments to Kennedy.
Following the 10 SRB propellant segments across the country will be the two aft skirts – which will ship to KSC in October 2017.
The two forward skirts will then follow in February 2018 ahead of SRB stacking operations in the VAB – which is currently slated to begin in March 2018.
(Images: NASA, Orbital ATK, L2 – via Philip Sloss)
Quelle: NS
-
Update: 30.09.2016
.
NASA Completes Welding on Massive Fuel Tank for First Flight of SLS Rocket
Welding is complete on the largest piece of the core stage that will provide the fuel for the first flight of NASA's new rocket, the Space Launch System, with the Orion spacecraft in 2018. The core stage liquid hydrogen tank has completed welding on the Vertical Assembly Center at NASA's Michoud Assembly Facility in New Orleans. Standing more than 130 feet tall, the liquid hydrogen tank is the largest cryogenic fuel tank for a rocket in the world. The liquid hydrogen tank and liquid oxygen tank are part of the core stage -- the "backbone" of the SLS rocket that will stand at more than 200 feet tall. Together, the tanks will hold 733,000 gallons of propellant and feed the vehicle's four RS-25 engines to produce a total of 2 million pounds of thrust. This is the second major piece of core stage flight hardware to finish full welding on the Vertical Assembly Center. The core stage flight engine section completed welding in April. More than 1.7 miles of welds have been completed for core stage hardware at Michoud. Traveling to deep space requires a large rocket that can carry huge payloads, and SLS will have the payload capacity needed to carry crew and cargo for future exploration missions, including NASA's Journey to Mars.
Quelle: NASA
-
Update: 6.10.2016
-
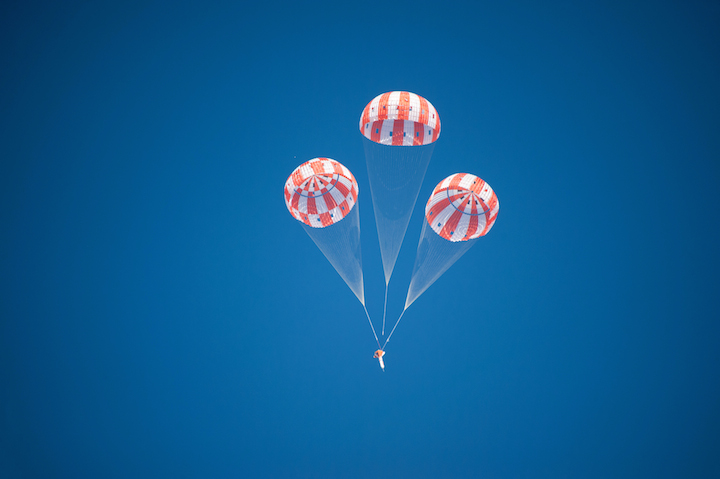
NASA successfully kicked off a series of tests Sept. 30 to qualify Orion’s parachute system for flights with astronauts, a milestone that will help the agency safely return crew to Earth from deep-space missions.
In the skies above the Arizona desert, a C-17 aircraft dropped a dart-shaped test article out of its cargo bay from 35,000 feet, or more than 6.5 miles, in altitude over the U.S. Army Yuma Proving Ground in Yuma to examine how the parachute system performed when conditions provided the highest dynamic pressure the parachutes have endured before.
As the test article fell from the sky, three small programmer parachutes initially deployed to reach the desired test conditions and were cut away to begin the Orion parachute deployment sequence. Two forward bay cover parachutes deployed to collect key data, and within seconds those parachutes were cut away and two drogue parachutes were deployed to stabilize and slow down the test article. The sequence continued when three pilot parachutes deployed to pull out the system’s three orange and white main parachutes that are used to slow Orion to a safe landing speed.
The dart-shaped test article was used because it can get to a higher velocity than the capsule-shaped article typically used in testing. When returning from missions in space, the parachute sequence normally begins at an altitude of 24,000 feet with the main parachutes fully deployed at about 4,000 feet.
“The parachute system performed as we expected and getting to this new stage of qualification testing is a real landmark as we prepare for Orion missions with crew,” said CJ Johnson, project manager for Orion’s parachute system at NASA’s Johnson Space Center in Houston. “We’ve had quite a few development tests up to this point to make sure we understand how the parachutes perform in various environments and potential failure scenarios, and this new series will give us confirmation of their performance for when the crew descends under the parachutes as they return from deep space destinations.”
Seventeen engineering development tests have already been completed. To qualify the parachute system for flights with crew, a total of eight tests, including this one, will be conducted over the course of about two and a half years. A capsule-like mockup will be used for six of the remaining tests, while a dart-shaped article will be used for one remaining test. NASA also is providing parachute test performance data to the agency’s Commercial Crew Program partners.
The next test of the parachute system is planned for October, when engineers will evaluate parachute performance when the capsule-shaped test article is dropped from 25,000 feet in altitude.
Orion will next venture into space during Exploration Mission-1 in 2018, an uncrewed mission atop NASA’s Space Launch System rocket, and will travel more than 40,000 miles beyond the moon. The parachute system will be delivered to NASA’s Kennedy Space Center in Florida at the end of this year for integration into the crew module for that test flight and will help the spacecraft slow down to a relatively gentle splashdown speed of about 17 mph in the Pacific Ocean after enduring reentry speeds of up to 25,000 mph as the spacecraft makes its way through Earth’s atmosphere. The first mission with astronauts is currently targeted for as early as 2021.
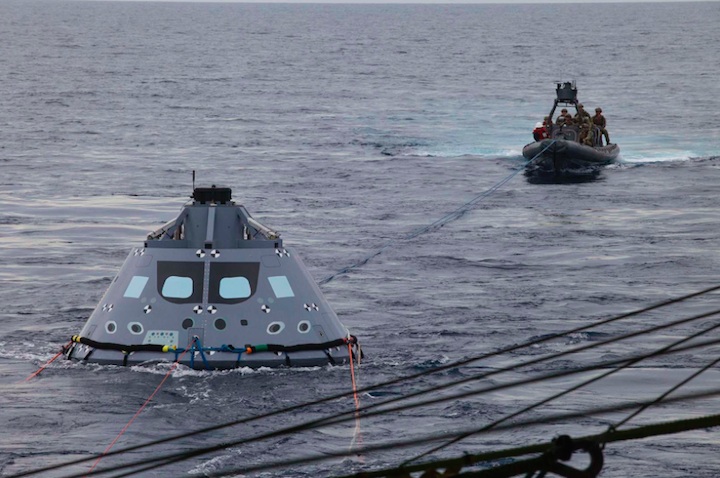
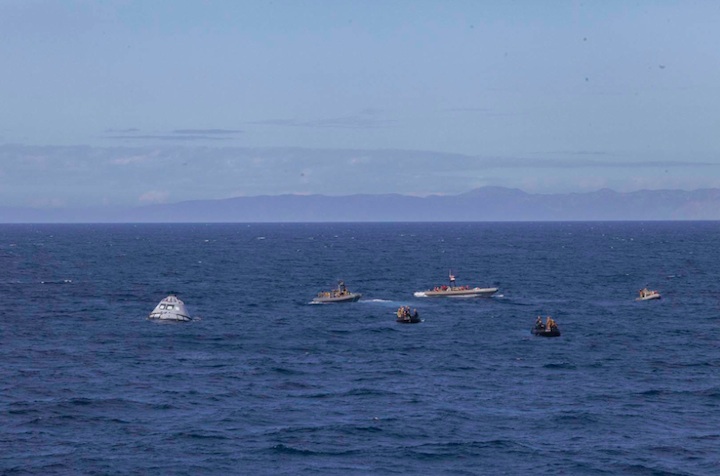
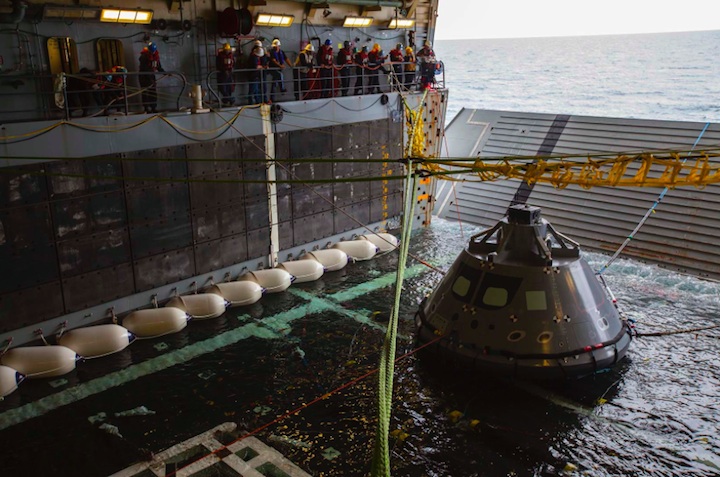
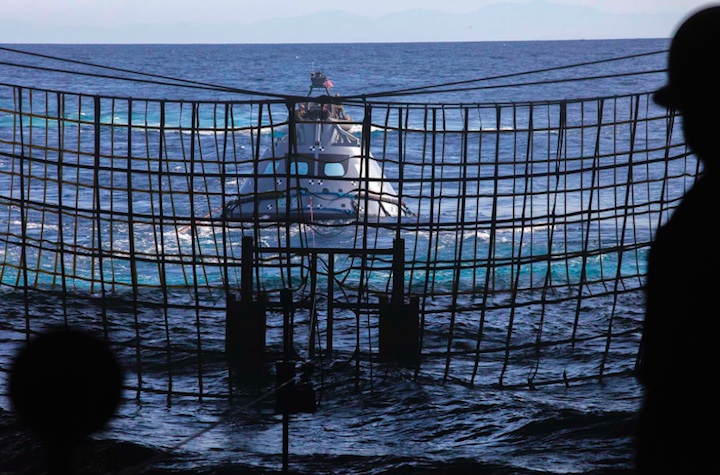