5.06.2020
ESA’s Prometheus is the precursor of ultra-low-cost rocket propulsion that is flexible enough to fit a fleet of new launch vehicles for any mission and will be potentially reusable.
At the Space19+ Council meeting in Seville, Spain last November, ESA received full funding to bring the current Prometheus engine design to a technical maturity suitable for industry. Developed by ArianeGroup, Prometheus is now seen as key in the effort to prepare competitive future European access to space.
By applying a design-to-cost approach to manufacturing Prometheus, ESA aims to lower the cost of production by a factor of ten of the current main stage Ariane 5 Vulcain 2 engine.

Features such as variable thrust, multiple ignitions, suitability for main and upper stage application, and minimised ground operations before and after flight also make Prometheus a highly flexible engine.
This Prometheus precursor runs on liquid oxygen–methane which brings high efficiency, allows standardisation and operational simplicity. Methane propellant is also widely available and easy to handle.
In the short term it is likely that operational engines will benefit from the application of Prometheus technologies.

Upcoming tests overseen by ArianeGroup at the DLR German Aerospace Center’s Lampoldshausen testing facility in Germany will validate the hardware components for the first Prometheus engine test model (M1).
In preparation, the P5 test bench will gain a 250 cubic metre capacity propellant tank for methane. This will allow engineers to efficiently switch test configurations between Prometheus and Ariane 6’s Vulcain 2.1 main stage engine, also in development.
Main subsystems are being manufactured. The first elements built last year benefited from new methods such as additive layer manufacturing (ALM) which speeds up production, achieves fewer parts and greatly reduces costs.

ALM builds a structure layer by layer, which is much quicker and easier than the traditional process of cutting away bulk material. Complex, optimised parts, impossible to manufacture via classical methods, can be created using less material and energy, and in far fewer manufacturing steps.
Components manufactured and now ready to test include the turbo pump’s turbine, pump inlet and gas generator valves. March will see the delivery of the chamber valves and on-board rocket engine computer for engine management and monitoring – the part that makes this a ‘smart’ engine and potentially reusable.
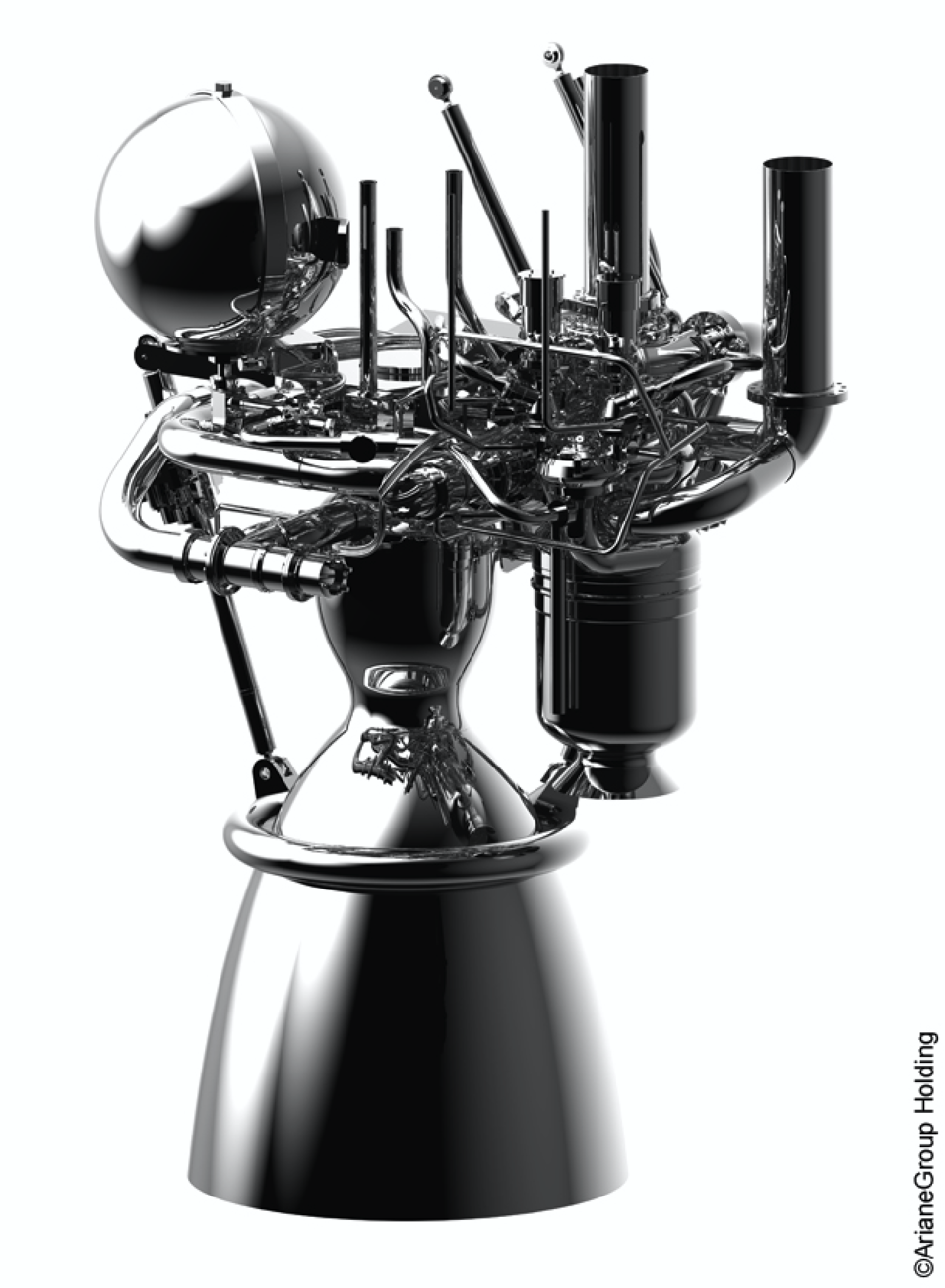
The first combustion chamber model is expected at the end of June while the combustion chamber for M1 will be delivered in December 2020.
Engineers will assemble the M1 full-scale demonstrator at the end of this year for testing on the ground in 2021.
Further Prometheus engines will be built for testing into the future.
Also within ESA’s Future Launchers Preparatory Programme, Arianeworks is currently preparing an in-flight reusable vehicle demonstration called Themis, which will incorporate the Prometheus precursor engine.
Prometheus represents a breakthrough in terms of cost and manufacturing and its robust design is the baseline for future evolutions of Ariane to 2030.
Quelle: ESA